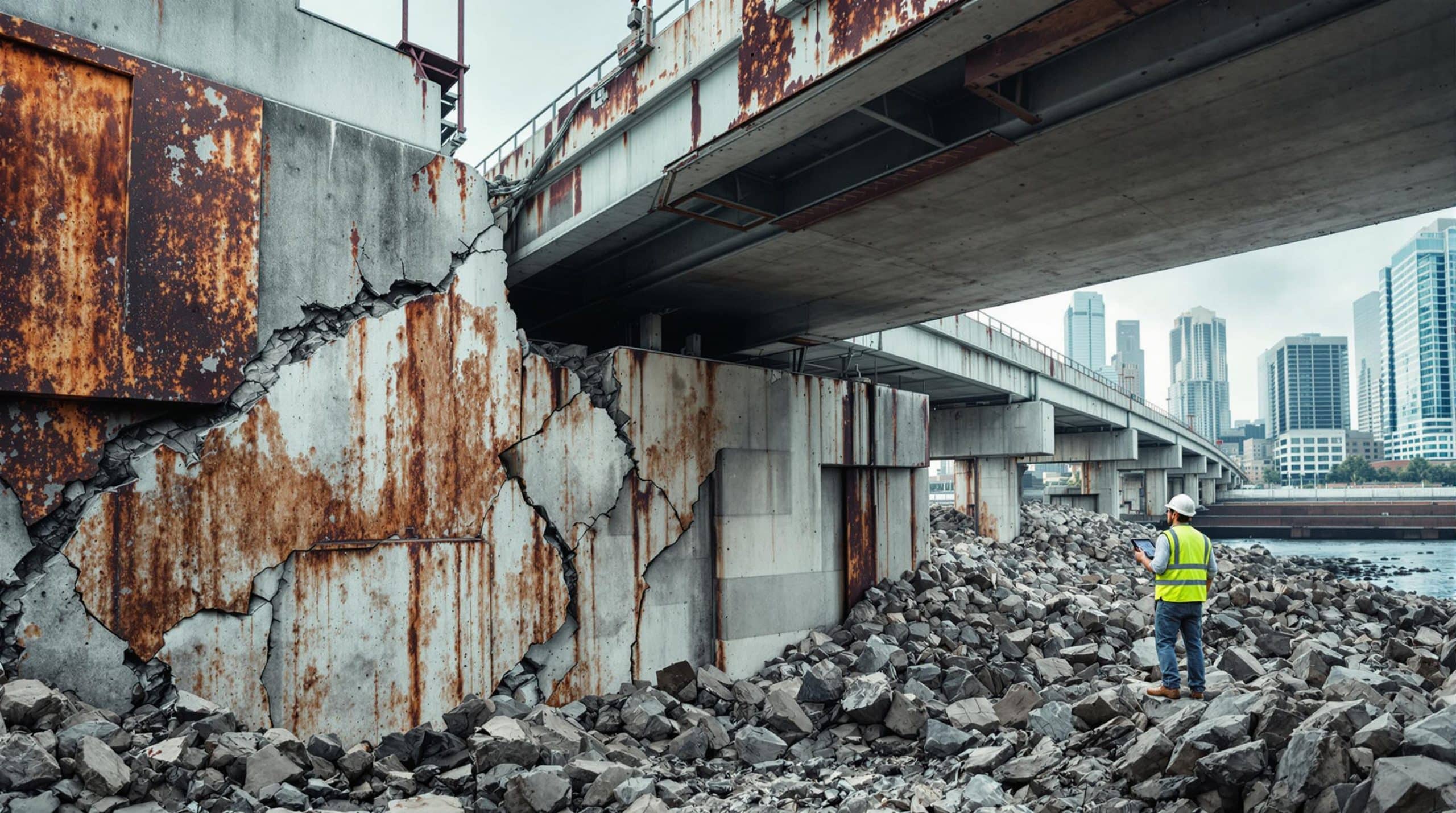
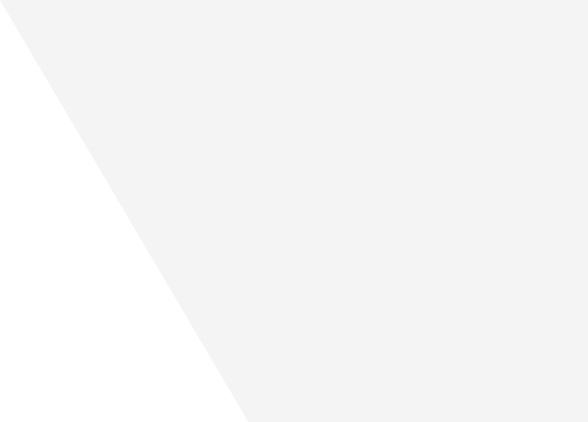
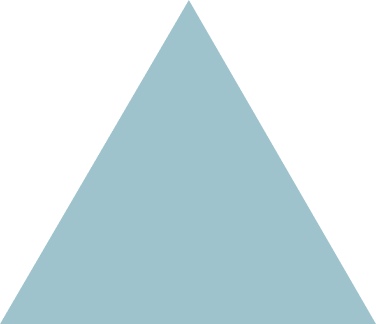
Aging infrastructure in the U.S. is a growing issue, with over $1 trillion in repair backlogs and severe consequences for the economy, safety, and environment. Water main breaks occur every 2 minutes, wasting 6 million gallons of treated water daily. If unaddressed, outdated infrastructure could cost the U.S. $7 trillion in lost business sales and $4 trillion in GDP losses by 2025. Climate change further worsens the problem, causing more frequent failures and higher maintenance costs.
Oxand Simeo™ offers predictive maintenance tools to reduce costs, prevent failures, and improve efficiency:
Aging infrastructure in the U.S. creates both operational headaches and financial burdens. Tackling these issues demands a shift toward predictive maintenance strategies.
As infrastructure ages, maintenance costs continue to climb.
Here’s how it impacts finances:
For example, in Mobile, Alabama, Mayor Sandy Stimpson inherited a $250 million deferred maintenance backlog in 2013 [4]. These costs often snowball when severe equipment failures occur.
Aging systems are more prone to breakdowns, which lead to more than just repair bills:
Take the 2018 Camp Fire in California as a stark reminder. This tragic wildfire, the deadliest in the state’s history, was caused by outdated electrical infrastructure [5]. Such disasters highlight the urgent need for modern safety measures.
As infrastructure ages, keeping up with modern regulations becomes increasingly difficult. Older systems often fall short in areas like:
Compliance Area Key Challenges Environmental Standards Struggles to meet stricter wastewater and stormwater regulations [6]. Safety Regulations Many older buildings fail to comply with today’s building codes [7]. Capacity Requirements Legacy systems can’t handle growing population demands [6]. Monitoring Systems Outdated equipment lacks advanced safety monitoring technology [8].The scope of the problem is massive – an estimated $150 billion investment is needed over the next 20 years just to bring U.S. infrastructure up to current standards [6].
Managing aging infrastructure demands a solid, data-based approach. Oxand Simeo™ uses a model-driven system that relies on historical data rather than just real-time IoT inputs. It incorporates over 10,000 predictive models and 30,000 maintenance rules, built on decades of expertise [2].
One example is its application for the French Ministry of the Armed Forces. The software analyzed 31 million ft² of built surfaces, 2 billion ft² of unbuilt surfaces, and more than 80,000 structures, with a total value exceeding $16.3 billion [9]. This helped determine the best strategies for investments and asset disposal.
Oxand’s predictive maintenance approach helps reduce expenses while improving asset performance:
Area Improvement Maintenance Costs 10–15% savings through risk-based optimization Component Lifecycle Up to 25% cost reduction for specific components Overall Savings Potential savings of up to 30% Energy Efficiency Boosted through targeted upgradesThese results stem from automated decision-making and data-driven investment strategies. The focus is on balancing cost savings with performance improvements, while also maintaining strong risk management and meeting compliance requirements [2].
Beyond cost and performance benefits, Oxand Simeo™ ensures assets meet evolving compliance standards. The system is designed to align with ISO 55001, introduced in 2014, through two main capabilities:
Reactive maintenance often leads to higher risks and expenses. According to a McKinsey report, predictive maintenance could help organizations save up to $630 billion in unnecessary costs by 2025 [12]. Let’s break down the differences between traditional reactive methods and modern predictive approaches.
This comparison highlights how predictive maintenance can improve both operational efficiency and financial outcomes.
For example, in the energy sector, a predictive system accurately forecasted compressor downtime with 80% precision, providing a 30-minute warning and generating over $1 million in production gains per site [14]. Similarly, Swedish utility Jämtkraft adopted ABB’s MNS Digital solution for predictive maintenance, enabling real-time monitoring, extending equipment lifespans, and streamlining maintenance schedules [15].
Predictive maintenance offers several clear advantages:
These benefits not only improve performance but also significantly reduce costs, making predictive maintenance a game-changer for modern infrastructure management.
Oxand’s predictive lifecycle management helps organizations lower costs, minimize downtime, and make better use of resources for aging infrastructure. Here’s what companies have achieved using this approach:
One example is Mueller Industries, which overhauled its maintenance process using handheld contact microphone sensors linked to a cloud-based system. By leveraging machine learning, they detected critical issues like rapid bearing wear on high-speed equipment, enabling timely repairs with minimal disruption [19].
These outcomes highlight the effectiveness of a structured approach, such as Oxand Simeo™.
Oxand Simeo™ offers data-driven tools to help you tackle the challenges of aging infrastructure. To make the most of it, follow these steps:
1. Initial Assessment
Start by documenting your current maintenance costs, downtime, and compliance data. This baseline will help you measure ROI as you implement changes.
2. Strategic Planning
Create an asset strategy that uses predictive analytics to plan maintenance, allocate budgets to critical assets, and track performance and compliance.
3. Implementation Framework
Phase Action Items Expected Outcomes Setup Document asset inventory and risk framework Clear understanding of assets Integration Install monitoring systems and train staff Real-time tracking Optimization Apply predictive maintenance schedules Lower maintenance costs Evaluation Monitor KPIs and refine strategies Better asset performanceMost organizations see results within 6-12 months, with ROI potentially reaching up to ten times the initial investment [19].